Numerical simulation of aluminum alloy quenching by direct thermal-mechanical coupling method and evolution of the elastic-plastic area
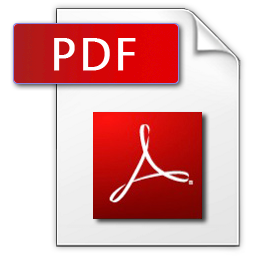
Luo Jiayuan1, Shi Chengxiang2
COMPUTER MODELLING & NEW TECHNOLOGIES 2013 17(5D) 19-23
1School of Mechatronics and Automotive Engineering, Chongqing Jiaotong University , Chongqing 400074, China
2Department of Mathematics and Information Engineering, Chongqing University of Education, Chongqing 400065, China
7075 aluminum alloy plate quenching process is simulated using direct thermal-mechanical coupling method, and the corresponding experimental results verify the numerical simulation with high accuracy. Based on the simulation results to study the Variation in the aluminum alloy plate during the quenching process, such as the conversion law between tensile stresses and compressive stresses and the evolution of elastic-plastic deformation area, and these two changes have been compared and analyzed, the results show that, there is always a transition region in the aluminum alloy plate during the quenching process, the region has very small or zero plastic strain, and the quenching residual stress extremes occurs in the region. The existence of the transition region is leading to the quenching residual stress distribution along the thickness direction has "turning point" and is the main reason for the W-shaped distribution.