Analysis of thermal-mechanical coupling and structural optimization of continuous casting roller bearing
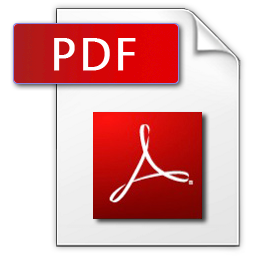
Disi Chen1, Gongfa Li1, 2, Honghai Liu2*, Guozhang Jiang1, Jia Liu1, Ze Liu1, Weiliang Ding1, Wei Miao1, Zhe Li1
1College of Machinery and Automation, Wuhan University of Science and Technology, Wuhan 430081, China
2Intelligent Systems & Robotics Group, School of Computing, University of Portsmouth, Portsmouth, PO1 3HE, United Kingdom
The continuous casting roller bearing was one of the important parts of continuous caster [1], its working temperature was relativity high, the working load was also very large and the working condition was complex. Since the external heat of casting roller bearings was much higher than internal, the continuous casting roller bearing was different from the general high-speed rolling bearing with heavy load. If the external heat that the bearing suffered could not dissipate in time, the extreme high working temperature might accelerate the failure of the bearing and severely reduce the productivity of the caster. To optimize the thermal structure of the continuous casting roller bearing, the thermal coupling analysis of the bearing should be conducted. Firstly, the stress field of the working continuous casting roller bearing should be analysed by ANSYS and the three-dimensional geometric CAD model and the CAE model of it should be established. Then find out the location where the bearing suffered the largest force by stress analysis, in the case of bearing block with cooling water, load the working temperatures to the bearing, after analysing, the result showed that the external temperature was the main contributor of internal stress, and the rolling element was the part inside of the bearing, which suffered the largest stress. To optimize the structure of the continuous casting roller bearing, the rolling element was turned into axial hollow structure, which could reduce the extreme stress of the rolling element bearing. By analysing all the maximum thermal stress of rolling element in different feasible hollowness, and finally the most suitable hollowness could be found out. The analysis results above showed that the optimization of the rolling element structure of the bearing could effectively reduce the internal stress and improve reliability of bearings in high working temperature. The conclusion of this study was significant in bearing optimizing or designing.