PREDICTION MODEL OF RECAST LAYER THICKNESS IN DIE-SINKING EDM PROCESS ON TI-6AL-4V MACHINING THROUGH RESPONSE SURFACE METHODOLOGY COUPLED WITH LEAST SQUARES SUPPORT VECTOR MACHINE
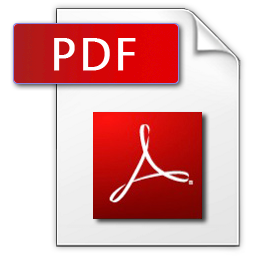
Jun Li, Xiaoyu Liu, Shiping Zhao
School of Manufacturing science and Engineering, Sichuan University, Chengdu 610065, P. R. China
Ti-6Al-4V is widely applied in frontier for its excellent properties such as a high strength-weight ratio, great heat stability and exceptional corrosion resistance. Electrical discharge machining (EDM) is suitable for machining titanium alloys, because it is the technical that removal materials by discharge energy and non-contact in processing progress. The recast layer is formed by the solidification of molten metal on the machined surface during the EDM process. In the present investigation, a hybrid approach using Least squares support vector machines (LS-SVM) and response surface methodology (RSM) for predication the recast layer thickness is proposed. Experimental plan is performed by response surface method with 20 experimental runs. The different machining parameters of pulse current, pulse on-time, and pulse off-time are selected as input factors. The white layer thickness (WLT) is response variable. The LSSVM method is applied to construct the predication model based on the orthogonal experiment swatches. The randomly 15 experimental runs were utilized to train the LS-SVM model to predict the WLT. Finally, support vector machine is used to compare with the proposed method. The proposed model can be good performance in prediction of white layer thickness of the complex EDM process.