Modelling and simulation of CNTs- and GNRs-based nanocomposites for nanosensor devices
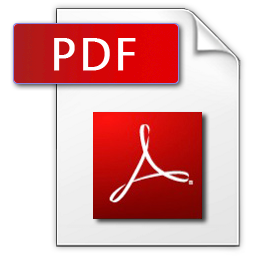
Y Shunin1, 4, S Bellucci2, Y Zhukovskii1, T Lobanova-Shunina3, N Burlutskaya4, V Gopeyenko4
COMPUTER MODELLING & NEW TECHNOLOGIES 2015 19(5A) 14-20
1Institute of Solid State Physics, University of Latvia, Kengaraga Str. 8, LV-1063 Riga, Latvia
2INFN-Laboratori Nazionali di Frascati, Via Enrico Fermi 40, I-00044, Frascati-Rome, Italy
3Riga Technical University, Institute of Avionics, 1 Lomonosov, Bld V, LV-1019, Riga, Latvia
4ISMA University, 1 Lomonosov, Bld 6, LV-1019, Riga, Latvia
The main objective of the current study is to demonstrate the implementation of advanced simulation models providing a proper description of the electronic properties, electrical conductivity, electromagnetic and electromechanical phenomena of functionalized CNT- and GNR-based nanostructures of different morphologies and their interconnects for nanosensor and nanomemory systems. The sensitivity of the local electronic density of states to external influences (mechanical, chemical, magnetic, etc) on the fundamental electromagnetic properties of CNTs, GNRs and their metal interconnects have been analyzed from the point of view of nanosensor applications. Nanoporous systems are considered as complicated ensembles of basic nanocarbon interconnected elements (e.g., CNTs or GNRs with possible defects and dangling boundary bonds) within the effective media type environment. The model of nanocomposite materials based on carbon nanoсluster suspension (CNTs and GNRs) in dielectric polymer environments (e.g., epoxy resins) is regarded as a disordered system of fragments of nanocarbon inclusions with different morphologies (chirality and geometry) in relation to a high electrical conductivity in a continuous dielectric environment. The electrical conductivity of a nanocomposite material depends on the concentration of nanocarbon inclusions (in fact, carbon macromolecules). Various nanocomposite morphologies are considered and computer simulation results are discussed.